New Blown-Film Cooling Technologies Set to Debut at NPE2024
Cooling specialist Addex to roll out new auto-profiling air ring for rotating dies, and new single-plenum air ring.
Addex is taking the wrap off two new products for blown film cooling at NPE2024, May 6-10, in Orlando, Florida, Plastics Technology has learned exclusively.
One is an auto-profile system for rotating dies, based on its high-resolution EGC (external gauge control) air ring, that’s capable of reducing gauge variation by 50%. It’s already in operation on a single-layer line at a Crayex plant in Georgia, and at another undisclosed film processor in South Carolina. While rotating dies are perceived by some as passé, the fact is there are many still in operation, according to Addex CEO Bob Cree, particularly on blown film lines making stretch films. Cree adds, “We see them operating in companies big and small. And many companies running rotating dies think the only way they can improve thickness variation is to buy a new line.”
The new air ring system operates similarly to Addex’s gauge-controlling EGC-based systems, which are commonly found on stationary dies, but with several added enhancements. Addex previously was able to achieve industry standard (for a stationary die) 50% reduction in gauge variation on rotating dies only by combining the EGC system with its internal bubble cooling (IBC)-based cousin, the Internal Gauge Control (IGC).
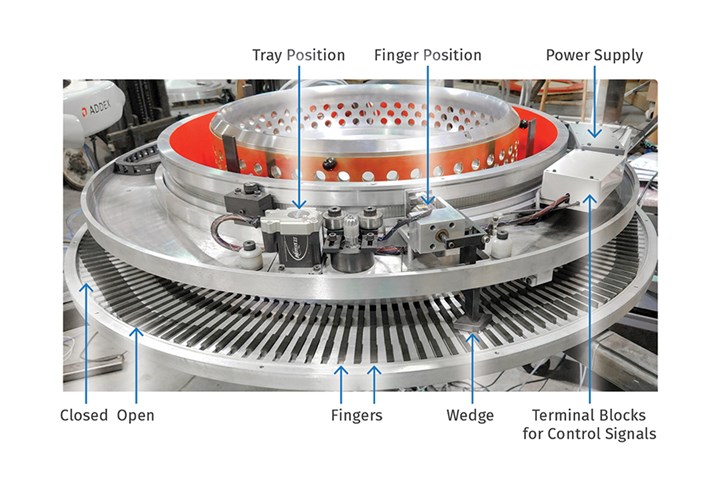
At NPE2024, Addex will debut a new External Gauge Control air ring for blown film applications utilizing rotating dies. A 12-in. air ring will have as many as 168 control zones. “Fingers” open or close to direct more or less cooling air to specific locations on the bubble as needed. Source: Addex
But with the new system, the IGC is no longer required. This significantly cuts the cost of a system down to the same range as conventional systems on stationary dies, but with the same performance achieved with the IGC add-on.
In the new air ring, air volume is controlled by a series of “fingers” that open or close to put more or less cooling air on the film, which thickens or thins the film out. On a 12-inch air ring, there are 168 control zones, with 200+ control zones on larger systems. But the real key to this new technology is a proprietary mapping algorithm. When combined with Addex’s third-generation controller, software and hardware package, the system regulates not only the air ring but also the die rotation.
Explains Cree, “On lines with oscillating haul-offs, the film is turning at the top, creating a twist that most processors have heard about, but in this case the die is fixed. It’s easier to make proper adjustments if the die is stationary, but rotating dies add another dimension to the auto-profile process that throws a huge monkey wrench into algorithm calculations.”
Adds Gautam Jagannathan, Addex’s software specialist and senior field service engineer, “Our control algorithm now has to compensate not only for the twist but also the die rotation, which turned out to be a serious mind-bender. The industry standard mapping capability is ±5 degrees for stationary dies, but we are getting ±1 degree of mapping even on rotating die systems, including both the twist and the die rotation, and that’s something that nobody else can do.”
Addex’s first foray into auto-profiling for blown film dates back to the 1990s, when it installed a system at a blown film processor that was using the company’s IGC. At that time, Cree recalls, “The control algorithms for the IGC were different from today’s EGC, so when we combined the two systems, it was a very difficult task to get them to work together without fighting each other, but ultimately we effectively reduced thickness variation by 50% on rotating dies.”
“Our goal here for rotating die was to try to hit the 50% reduction in gauge variation.”
He adds, “But it was quite expensive for the customer and was complicated for Addex to program. The customer had to buy two auto profiles, and you can imagine the math of trying to figure out how to separate those two control algorithms from each other. It was a problem, and we stopped doing it. But we knew there was an opportunity because of the number of rotating dies still in the market and the fact that other OEMs were having limited success putting auto profiling on these lines.”
So, about two years ago, Addex began talking with blown film processors with rotating dies that needed to improve film quality but couldn’t justify investing in a brand-new line to do so. “We kept hearing from our customers that they needed more quality from the lines they had —that because of the quality push in the industry and the move toward sustainability, they needed to get better film without breaking the bank. One of my biggest customers has a lot of rotating dies, so we were motivated, and we dusted off all of our old notes to take a fresh look at the problem, and installed our first auto-profiling EGC air ring-only system (no IGC) on a rotating die line at the plant in South Carolina last March. And the feedback from them was that the quality improvement was dramatic.”

Last December, Addex retrofitted its External Gauge Control air ring on this line at film processor Crayex, which runs rotating dies.
Jagannathan, who started up that system, adds, “Our goal here for rotating die was to try to hit the 50% reduction in gauge variation. I don’t think previous auto-profile, air-ring technologies from other vendors for rotating dies were anywhere near 50%; maybe 20-25%. But we’re seeing 50%.” And, as Cree notes, on top of boosting quality reducing film-thickness variations, this result also cuts material costs and provides a pathway for a film processor to meet its sustainability goals.
Addex, however, learned something significant on this first retrofit in South Carolina that they applied to the second, more recent system installation at Crayex in Georgia, which took place in December 2023. For the South Carolina film processor, Addex basically integrated the auto-profile air ring into the processor’s existing die rotator. But the modularity of its Gen3 control package enabled Addex to go a step further with Crayex.
Jagannathan states, “So now we are taking control of the die movement in concert with what we’re doing with the traditional mapping, and that is the system we installed at Crayex.” Jagannathan says that because of the next-generation control technology, the Crayex line appears to be outperforming the line at the South Carolina processor.
Cree adds that the South Carolina processor has ordered two more air rings now with the third-generation control package. The first of these will start up in March. In addition to the two units already in the field, Addex is beta testing the Generation 3 EGC air ring systems at a total of four locations, tweaking the technology to enhance its performance with each startup.
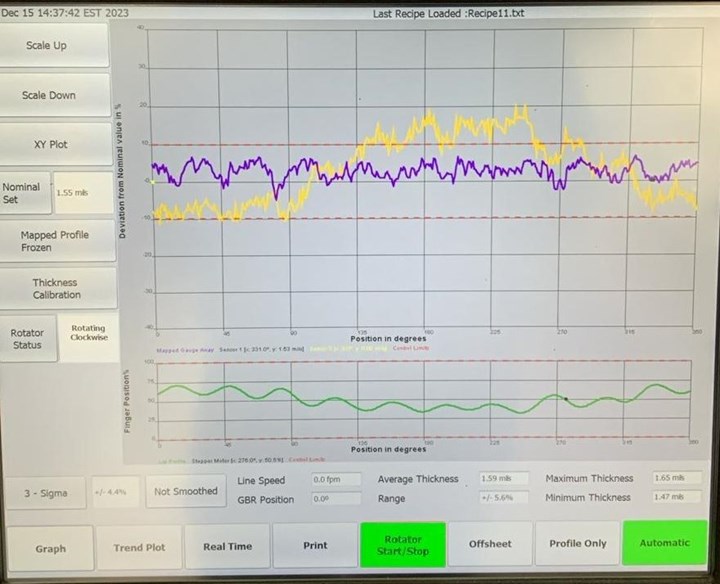
Fillm processor Crayex drastically reduced thickness variations once the Addex gauge-controlling air ring was installed.
Adds Bill Wilck, Addex’s production manager, “The compact Gen3 controller is really simple and easy to work with — it’s no bigger than a small bread box — and it’s also modular, so we can mix-and-match modules with capabilities to not only control the rotation of the die but also to monitor for bubble breaks, inflate/deflate the tube (for non-IBC lines) or even control the IBC.”
New Single-Inlet Plenum
At NPE2024, Addex will also debut its first-ever air ring with a single-inlet
plenum design. While multi-inlet air rings have conventionally outperformed their single-inlet counterparts because they provide more uniform air distribution, Addex got input from film processors that running just one hose rather than the 4, 6, 8 or 10 that are typical of multi-plenum designs would be beneficial.
Says Josiah Austin, Addex’s mechanical and field service engineer, “With air rings being height-adjustable to help generate more output, it becomes imperative you get rid of all the hoses because it can be a nightmare pulling all of them up and down. Also, we have been supplying air rings to other machine builders and they like the line to look as neat as possible. So, we figured it would be really nice if we could clean that area up.”
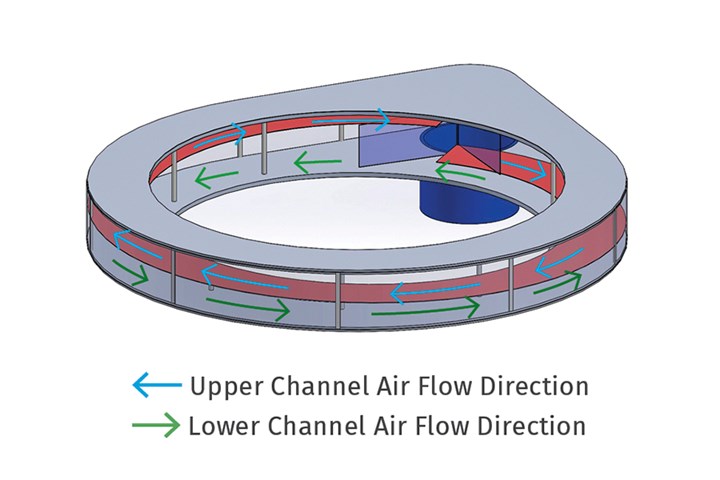
Image shows the internal design of Addex’s new single-plenum design to more uniformly distribute air flow. Notice one circular channel flowing clockwise all around, and a second going in the opposite direction all the way around.
Single-inlet air rings can be especially troublesome on lines without automatic thickness control. Cree says, “Automatic units can compensate for any gauge variations caused by erratic air-flow distribution, and you can actually see the required inlet related compensating control effects in the system, so lacking automatic profile control can be a problem.”
So Addex set a goal to design a single-inlet plenum that performed equal to what it had achieved with its multi-inlet conventional plenum. Its solution was to apply a regular division design inspired by Dutch artist M.C. Escher, in which irregular shapes, or combinations of shapes, interlock completely to cover a surface or plane. According to Cree, what Addex devised is a patent-pending, dual-counterflow plenum design with one circular channel flowing clockwise all around, and a second going in the opposite direction all the way around. This creates the Escher “equal and opposite” effect, resulting in uniform combined air flowing through the air ring.
Wilck adds, “Most other single-inlet plenums are shaped like a Nautilus: machined in a spiral that starts off big, gets smaller as it goes around, and is smallest at the very end. But because of all of the constantly changing radiuses, these types of plenums can be extremely expensive to make. In fact, it’s actually so expensive to make the plenum that way that it has made the single-plenum air rings significantly more expensive compared to multiple-plenum ones. The channels in this new design are round, therefore it becomes much easier to make.”

New air ring from Addex has a single-inlet plenum, eliminating the problem moving multiple hoses up and down to accommodate height-adjustable units.
At its pilot line in Newark, N.Y., Addex switched between the new single-inlet design and the multi-inlet unit, both without auto-gauge control, and notes the single-inlet plenum provided better overall thickness profile with reduced variability. “This was unexpected, and it also appeared to create less turbulence with better bubble stability,” Austin adds. “With multi-inlet plenums, you have inlet hitting another inlet, hitting another inlet, and you get repeating cases of internal turbulence. In addition, the hose length and bend variations also common to multi-inlet plenums are all gone with the single-inlet plenum, so this coupled with the equal and opposite flows leads to significantly better overall performance.”
Related Content
Cooling the Feed Throat and Screw: How Much Water Do You Need?
It’s one of the biggest quandaries in extrusion, as there is little or nothing published to give operators some guidance. So let’s try to shed some light on this trial-and-error process.
Read MoreFully Automated Extrusion Process Enables Use of Composites for Manufacturing Pressure Tanks
Amtrol was looking for a more cost-effective means to produce thin-wall liners for a new line of pressure tanks. With the help of a team of suppliers, they built one of the world’s most sophisticated extrusion lines.
Read MoreUnderstanding Melting in Single-Screw Extruders
You can better visualize the melting process by “flipping” the observation point so that the barrel appears to be turning clockwise around a stationary screw.
Read MoreWhy Compression Ratio is Important
Compression ratios have been pretty much standardized over the years, based on what has typically worked before. But there are quite a few variables that must be considered in order to get the optimum performance from your screw.
Read MoreRead Next
Why (and What) You Need to Dry
Other than polyolefins, almost every other polymer exhibits some level of polarity and therefore can absorb a certain amount of moisture from the atmosphere. Here’s a look at some of these materials, and what needs to be done to dry them.
Read MorePeople 4.0 – How to Get Buy-In from Your Staff for Industry 4.0 Systems
Implementing a production monitoring system as the foundation of a ‘smart factory’ is about integrating people with new technology as much as it is about integrating machines and computers. Here are tips from a company that has gone through the process.
Read MoreUnderstanding Melting in Single-Screw Extruders
You can better visualize the melting process by “flipping” the observation point so that the barrel appears to be turning clockwise around a stationary screw.
Read More