Variable-Diameter Air Ring Cools Film Above Frost Line
Tower-mounted adjustable ring adds cooling so that blown film can run at optimum line speeds with structures having soft inner skin layers that tend to block.
VarDAR Systems Ltd of the U.K. is offering blown film processors a novel type of variable-diameter, dual-directional-flow air ring that is tower mounted, providing cooling above the frost line to permit processors with a shorter-than-desirable nip height to improve productivity. The company designed and developed the air ring three years ago for Echo Packaging, a U.K.-based, family-owned processor of high-performance blown films.
Echo now has two such systems in operation at its plant. Says Kishan Nanji, director of Echo Packaging, “The VarDAR system has enabled us to maximize the capacity of our line by 20-25%. The system was developed and tested from its early stages with the help of our engineers and operators. We like the simplicity and benefits it provides.” VarDAR says systems are also running at blown film plants in France, Germany, Austria, Italy, and the U.S.
The new air ring can be provided on a retrofit basis directly from VarDAR. For new installations, it is available exclusively from Hosokawa Alpine, fully integrated into its control systems. VarDAR has the system running on a line at the Hosokawa Alpine Technical center in Augsburg, Germany. The VarDAR air ring is said to be ideal on structures with that have soft inner skin (sealing) layers, which tend to block. In the case of PE structures, the VarDAR has been shown to reduce the surface temperature of the film from 180°F to about 150°F.
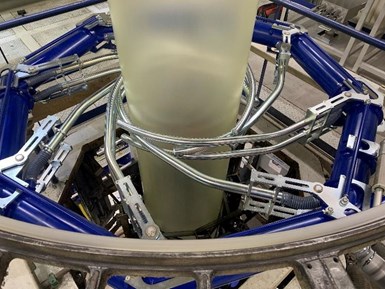
The VarDAR air ring is typically mounted above the main calibration basket and the oscillating gauge. (Photos: VarDAR Systems LLC)
Reducing Blocking and Tackiness
The VarDAR air ring is typically mounted above the main calibration basket and the oscillating thickness gauge, if so equipped. It generates an even curtain of cooling air that flows both in a downward and upward direction onto the film surface. The VarDAR ring uses multiple curved “blades” that ensure an even curtain of air surrounds the bubble around its total circumference.
Each blade is mounted into the frame with integrated air distribution, making the system compact and easily accessible for cleaning. The VarDAR is controlled by a PLC, which manages the gap between the blades and the bubble surface, automatically turning the air off when the line is shut down and retracting the blades to a home position.
According to the company, adding additional cooling above the frost line reduces effects such as blocking, which occurs when the inside surface of the bubble sticks to itself at the nip during collapsing, making it nearly impossible to open. This system also reduces tackiness of the bubble’s outer surface when still hot. Explains Andrew Barnes, who heads up sales and marketing for VarDAR, “Sometimes, you run a product where, because of blocking, you have to slow down the line to achieve a manageable production rate. Usually these are products that have a softer material on the inner skin layers, typically used to help welding in later downstream processes.”
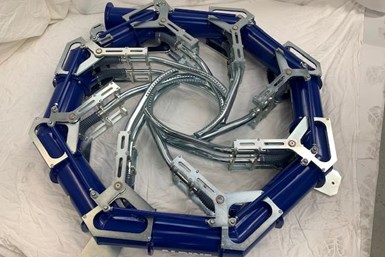
The VarDAR uses multiple curved “blades” to ensure an even curtain of air surrounds the bubble.
He continues, “An extreme example of this is running VLPDE or plastomers on the inner bubble surface to create a surface with low heat-seal initiation temperature for form/fill/seal (FFS) applications. To get an idea of what is achievable, you simply take the difference between the output that can be achieved as a blocked tube and your current manageable production rate. This can represent up to a 15-30% production gain on modern machinery.”
Barnes cautions that the VarDAR is not designed to increase the output of a blown film line, but to recover lost output caused when processors slow down the line to eliminate blocking.
Reducing the blocking effect also makes the film easier to handle downstream because it is easier to separate. “Splitting the web can be terribly frustrating for machine operators, and the easier it is to separate the film, the higher the output of the production line will be,” says Barnes. Not only is splitting blocked film frustrating, but it can generate scrap. The VarDAR system reduces scrap levels due to better control of trims and easier web splitting. It can also improve the aesthetics of the film because it reduces the stretching and creasing inherently caused by the slitting and separating processes typical of blocked films.
VarDAR Systems CEO Andrew Parker says blown film processors that have equipped lines with its tower-mounted system are realizing gains that include:
• Significant increases in productivity;
• Quicker setup times;
• Reduction in blocking and scrap levels, providing better separation of film and efficient slitting;
• Lower percentage of expensive masterbatches needed to produce quality film because less anti-block additive is needed;
• Reduced creasing and improved flatness, resulting in better finished reel geometry;
• Improved overall appearance of the film because of less stretching and creasing in the processing of films prone to blocking.
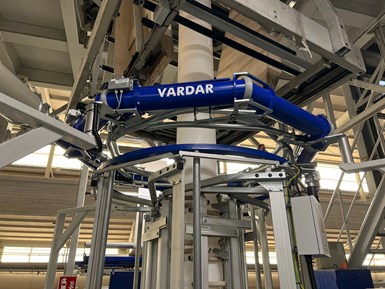
Cooling the bubble above the frost line means that processors running films that tend to block no longer have to slow the line down.
The tower-mounted systems are available in five different frame sizes, and each can cover a range of blow-up ratios, from small tube lines for shipping sacks to large machines with web widths of up to 10 ft. Because it cools the film above the frost line, the VarDAR system does not interfere with any of the existing systems that control the line, air ring, internal bubble cooling and/or film-thickness profile.
The VarDAR system tower-mounted systems are manufactured and shipped from the company’s plant in Cheltenham, England.
Related Content
Avoid Four Common Traps In Granulation
Today, more than ever, granulation is an important step in the total production process. Our expert explains a few of the many common traps to avoid when thinking about granulators
Read MoreUnderstanding the ‘Science’ of Color
And as with all sciences, there are fundamentals that must be considered to do color right. Here’s a helpful start.
Read MoreFully Automated Extrusion Process Enables Use of Composites for Manufacturing Pressure Tanks
Amtrol was looking for a more cost-effective means to produce thin-wall liners for a new line of pressure tanks. With the help of a team of suppliers, they built one of the world’s most sophisticated extrusion lines.
Read MoreSpecialty Purging Compounds Optimize Color and Material Changeovers
Selecting of the correct purging compound can speed up material and color changeover time and reduce scrap. You’ll even save on material.
Read MoreRead Next
High-Output Air Ring for Heavy-Duty Bags
Air ring exceeds output rates of 1320 lb/hr and targets bags for form-fill-seal applications.
Read MoreRecycling Partners Collaborate to Eliminate Production Scrap Waste at NPE2024
A collaboration between show organizer PLASTICS, recycler CPR and size reduction experts WEIMA and Conair will seek to recover and recycle 100% of the parts produced at the show.
Read MoreBeyond Prototypes: 8 Ways the Plastics Industry Is Using 3D Printing
Plastics processors are finding applications for 3D printing around the plant and across the supply chain. Here are 8 examples to look for at NPE2024.
Read More