ENTEK Expanding in Machinery, Battery-Film Processing
Showcases new plant to support machinery business, announces plans to build bigger compounding extruder and lays out strategy to build two new battery-separator plants.
ENTEK announced in February that it is close to completing Phase 1 of its build out of the company’s new 100,000 ft2 manufacturing facility in Henderson, Nev. At the same time, the company disclosed it was building its largest compounding extruder ever and laid out its plans to build two new lithium-ion battery-separator film plants to meet demand in electric vehicle and energy-storage markets.
To date, ENTEK has invested $15 million in the facility has hired about 50 people, company officials said at a media briefing and plant tour in Nevada. The Henderson plant is temperature-controlled for both the precision machining equipment and for the comfort of its employees. It houses a machine shop with CNC machinery and equipment, along with in-house heat-treating capabilities to help ENTEK further reduce lead times and have more control over the processing of its parts. The Henderson plant also features fabrication and assembly, controls engineering and mechanical engineering departments.
Linda Campbell, v.p. of extrusion sales for ENTEK Manufacturing, said the new plant in Henderson will support its current customer base, buoy the company’s new wear-parts division for the twin-screw extrusion/materials compounding industry, and help the company reduce lead times and increase production of these parts.
The Henderson plant, for example, is expected to help ENTEK reduce by 50% the time it takes to produce and ship screw elements. “Increasing our manufacturing capabilities is important for us; we needed more space, and more workers, to keep up with our growth, including the growth of our wear parts business,” she said. “This expansion will help us meet our aggressive forecast for new business in the coming years.”
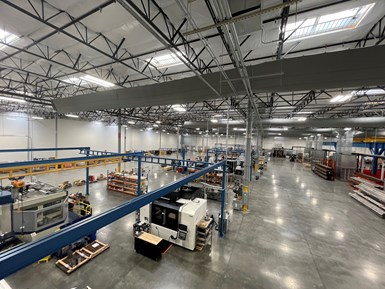
Photos: ENTEK
ENTEK will also use the new facility to support the continued growth of ENTEK Adaptive, the company’s material handling business that was formed in January 2022 when ENTEK bought Adaptive Engineering & Fabrication. ENTEK Adaptive makes material handling systems for difficult-to-convey materials.
In other news related to its machinery business, ENTEK said it has in development a 160-mm, 44:1 L/D twin-screw compounding extruder, which would be the largest machine in its product line. “We have been making replacement wear parts for this size of machine for almost 20 years for other brands of twin-screw extruders,” said Campbell. ENTEK recently introduced its first high-torque machine and said this new extruder may come with a high-torque option. The first 160-mm is scheduled to ship in the fourth quarter of 2024.
Concerning its battery-separator business, ENTEK laid out details for its $1.5 billion investment to build two new facilities in the U.S. The company currently makes separator film at its headquarters in Lebanon, Ore., as well as at facilities in the U.K., Indonesia and Japan. The recent recipient of $200 million in government funding for this project, ENTEK plans on building plants in Indiana — with Terre Haute as the targeted destination — and Alabama. ENTEK CEO Larry Keith said the company is the only U.S.-owned and U.S.-based producer of ‘’wet-process’’ separator for lithium-ion batteries. It uses non-chlorinated solvents to extract oil from the process.
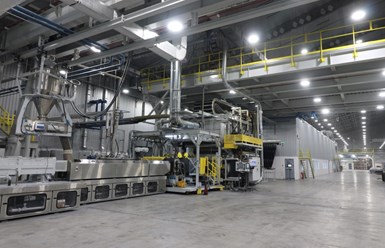
Keith said the first plant will open in 2025 with two production lines and a capacity to produce 1.4 billion meters2 of film, the equivalent of about 31 million lb.
If all goes according to plan, both the Indiana and Alabama plants with be equipped with 8-10 production lines each, with ENTEK Manufacturing supplying the extruders and ENTEK Adaptive upstream materials-handling systems. ENTEK recently signed a deal with Brückner Group USA to supply 18 biaxial-orientation systems for the lines.
Related Content
Fully Automated Extrusion Process Enables Use of Composites for Manufacturing Pressure Tanks
Amtrol was looking for a more cost-effective means to produce thin-wall liners for a new line of pressure tanks. With the help of a team of suppliers, they built one of the world’s most sophisticated extrusion lines.
Read MoreTroubleshooting Screw and Barrel Wear in Extrusion
Extruder screws and barrels will wear over time. If you are seeing a reduction in specific rate and higher discharge temperatures, wear is the likely culprit.
Read MoreHow Much L/D Do You Really Need?
Just like selecting the extruder size and drive combination, the L/D should be carefully evaluated.
Read MoreSpecialty Purging Compounds Optimize Color and Material Changeovers
Selecting of the correct purging compound can speed up material and color changeover time and reduce scrap. You’ll even save on material.
Read MoreRead Next
For PLASTICS' CEO Seaholm, NPE to Shine Light on Sustainability Successes
With advocacy, communication and sustainability as three main pillars, Seaholm leads a trade association to NPE that ‘is more active today than we have ever been.’
Read MorePeople 4.0 – How to Get Buy-In from Your Staff for Industry 4.0 Systems
Implementing a production monitoring system as the foundation of a ‘smart factory’ is about integrating people with new technology as much as it is about integrating machines and computers. Here are tips from a company that has gone through the process.
Read MoreRecycling Partners Collaborate to Eliminate Production Scrap Waste at NPE2024
A collaboration between show organizer PLASTICS, recycler CPR and size reduction experts WEIMA and Conair will seek to recover and recycle 100% of the parts produced at the show.
Read More