BASF Launches Innovative Catalyst to Process Renewable Feedstocks
CircleStar catalyst decreases CO2 footprint in the bioethylene value chain for products ranging from jet fuel to plastics.
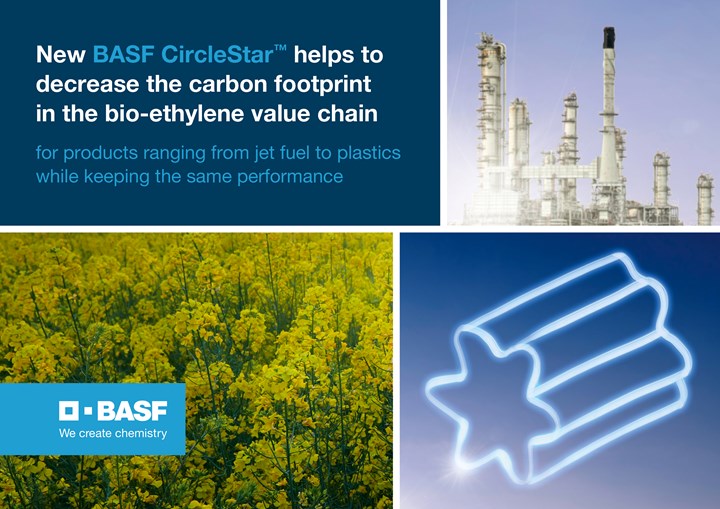
An innovative dehydration catalyst to process renewable feedstocks has been introduced by BASF. The star-shaped, CircleStar catalyst achieves a 99.5% selectivity for the ethanol-to-ethylene (E2E) conversion. With an operating temperature that is more than 75 F lower compared to conventional processes, CircleStar reportedly helps to decrease the carbon footprint in the bio-ethylene value chain for products ranging from jet fuel to plastics by more than 10% while maintaining the same performance.
This catalyst’s advanced performance is attributed to its unique star shape that maximizes the active geometrical surface area for the reaction. In addition, the packed density in the reactor bed is significantly lower compared to conventionally shaped catalysts, which impacts the overall cost optimization of the reaction. The novel geometry is also said to lead to a better mass transfer and a longer catalyst lifetime due to the beneficial operation temperature and pressure-drop profile.
The E2E process plays a fundamental role for the chemical industry to transform to climate neutrality and to achieve their net-zero targets. BASF has in-depth experience for more than 25 years in E2E with dedicated catalyst development and testing available. The existing ethylene is 99% fossil-based while the BASF E2E catalyst is offering the possibility to change the ethylene and its downstream value chain to make it biobased. In this process, CircleStar helps to further decrease the CO2 emissions in the biobased route by enabling lower temperature operations, longer lifetime and lower pressure drop in the catalyst bed.
Related Content
-
Why (and What) You Need to Dry
Other than polyolefins, almost every other polymer exhibits some level of polarity and therefore can absorb a certain amount of moisture from the atmosphere. Here’s a look at some of these materials, and what needs to be done to dry them.
-
Blend Amorphous PHA with PLA to Improve injection Molded Part Properties
Adding aPHA to PLA can boost a range of mechanical properties and expedite composting. Here are the details as well as processing guidelines for injection molding the blends.
-
Melt Flow Rate Testing–Part 1
Though often criticized, MFR is a very good gauge of the relative average molecular weight of the polymer. Since molecular weight (MW) is the driving force behind performance in polymers, it turns out to be a very useful number.