Injection Molding
In injection molding, material is fed through a hopper into a barrel where a reciprocating screw mixes and melts the material then injects it into a mold.
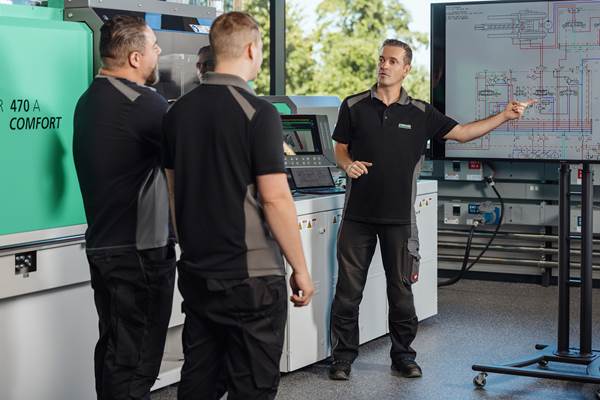
Narrow Your Injection Molding Search
ESSENTIAL READING
VIEW ALLHow To Design Three-Plate Molds – Part 4
There are many things to consider, and paying attention to the details can help avoid machine downtime and higher maintenance costs — and keep the customer happy.
Read MoreIs There a More Accurate Means to Calculate Tonnage?
Molders have long used the projected area of the parts and runner to guesstimate how much tonnage is required to mold a part without flash, but there’s a more precise methodology.
Read MoreBack to Basics on Mold Venting (Part 2: Shape, Dimensions, Details)
Here’s how to get the most out of your stationary mold vents.
Read MoreBack to Basics on Mold Venting (Part 1)
Here’s what you need to know to improve the quality of your parts and to protect your molds.
Read MoreHow to Design Three-Plate Molds, Part 1
There are many things to consider, and paying attention to the details can help avoid machine downtime and higher maintenance costs, and keep the customer happy.
Read MoreHot Runners: How to Maintain Heaters, Thermocouples, and Controls
I conclude this three-part examination of real-world problems and solutions involving hot runners by focusing on heaters, thermocouples, and controls. Part 3 of 3.
Read MoreLatest Injection Molding News And Updates
Automated Injection Molding Process Adjustments
Shibaura says its S-Concept represents an AI technology capable of making real-time process adjustments.
Read MoreEnhanced Temperature Controls for Hot Runners, Extrusion and Packaging
NPE2024: Athena introduces expanded hot-runner controller with up to 120 zones, plus updated panel-mount “universal” temperature/process control.
Read MoreNext-Generation All-Electric and Vertical Injection Molding Machines
Sodick Plustech’s VR-G and MS-G2 Series both utilize the company’s proprietary V-Line technology, separating plasticizing and injection functions, and have upgraded displays, energy efficiency, response time and more.
Read More3D Printed Hot Runner Nozzles, Pressure Pads Provide Reliable Temperature Handling
NPE2024: Witosa GmbH, through its distributor DMS, brings the Monolith hot runner nozzle and hardened steel Energy Blocker to the U.S., enabling the reduction in time, costs and improvements in product quality.
Read More'Simple' Units Feature State-of-the-Art Controls
NPE2024: New dryer line from Motan billed as the most cost-effective entry-level models it offers and comes equipped with state-of-the-art control technology.
Read MoreEnhanced Dry-Ice Cleaning Systems for Screws, Tooling
NPE2024: Cold Jet will be displaying four new dry-ice cleaning solutions for screw and tooling, and will also offer booth visitors a chance to win one of them.
Read MoreFeatured Posts
Absolute Haitian Brings Next Generation of Presses to Orlando
Absolute Haitian says Generation 5 of the servo-hydraulic Haitian and electric Zhafir machines lines emphasize efficiency, performance and intelligence.
Read MoreProcessing Megatrends Drive New Product Developments at NPE2024
It’s all about sustainability and the circular economy, and it will be on display in Orlando across all the major processes. But there will be plenty to see in automation, AI and machine learning as well.
Read MorePHA Compound Molded into “World’s First” Biodegradable Bottle Closures
Beyond Plastic and partners have created a certified biodegradable PHA compound that can be injection molded into 38-mm closures in a sub 6-second cycle from a multicavity hot runner tool.
Read MoreFour Industry 4.0 Tech Adoption Insights from Indiana Plastics Manufacturers
As more plastics manufacturers step into the Fourth Industrial Revolution, insights have emerged about how best to approach the digital transformation journey.
Read MoreHow To Design Three-Plate Molds – Part 4
There are many things to consider, and paying attention to the details can help avoid machine downtime and higher maintenance costs — and keep the customer happy.
Read MoreUnderstanding the Effect of Pressure Losses on Injection Molded Parts
The compressibility of plastics as a class of materials means the pressure punched into the machine control and the pressure the melt experiences at the end of fill within the mold will be very different. What does this difference mean for process consistency and part quality?
Read MoreFAQ: Injection Molding
Plastic injection molding is a cyclical manufacturing process that allows for cost-efficient production of a mass number of identical parts made from either thermoplastic or thermoset materials.
Cushion values in injection molding ultimately are an indication of a part’s quality, especially its dimensions. A consistent cushion will create consistent part dimensions.
It is important to determine which type of bubble your part has, and what the root cause might be. Determining bubble type will allow you to pinpoint the source and determine your next course of action to eliminate the problem.
Most molders are still relying on “general-purpose” screw designs that go back 30 years. With all of the technical improvements that have been made on machines over that time, nothing has been done to improve melt uniformity. We still use “general-purpose” (GP) screws, which well-known screw designer Bob Dray wisely has called “no-purpose” screws. That is they do not melt plastic uniformly. Processing with a uniformly melted plastic would seem like a high priority, but it has seen little if any attention.
Injection Molding Supplier Categories
- Thermoformers
- Injection Molding Machines
- Platens
- Thermoforming Molds
- Extrusion Blow Molding Machines
- Pre-expanders, Polystyrene Bead
- Trimmers, Deflashers for Blow Molding
- Stretch-Blow Molding Machines
- Nonferrous Metals for Molds
- Mold/Die Management Systems
- Injection Molds
- Mold Steels
- Injection Blow Molding Machines
- Dip-Blow or Compression-blow Molding Machines
- Cutting, Stamping, Trimming Dies
- Quick-mold-change Equipment
- Mold Making and Repair Equipment
- Injection Molding Nozzles
- Parison Programmers
- Mold Components
- Injection Blow Molds
- Presses, Polystyrene Bead
- Spray Coating Systems (for Bottles)
- Rotational Molds
- Inserts
- Accumulators (Melt)
- Structural Foam Machines (for Thermoplastics)
- Injection Molding Non-return Valves
- Mold Evacuation Systems
- Mold Grease
- Rotational Molding Machines
- Compression/Transfer Molds
- Mold-cleaning and Maintenance Chemicals
- Nonmetallic Tooling Materials
- Hot Runner Components
- Foam Molds
- Compression/Transfer Presses
- Prototype Molds